Newsletter Volume 4 Issue 1
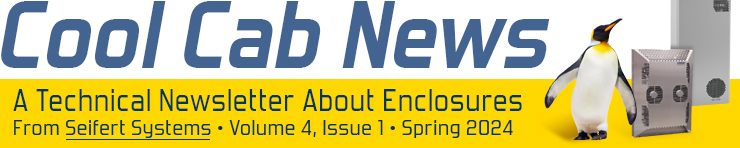
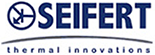
- When to Use Thermoelectric Coolers
- When to Use Thermoelectric Coolers
- Cooling Energy Storage Battery Enclosures
- Filter Fans
Featured video: https://www.youtube.com/watch?v=kX-5GIF-97s

When to Use Thermoelectric Coolers
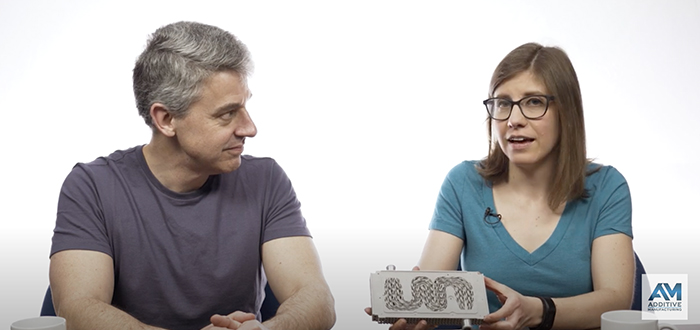
Screen capture of Peter Zelinski and Stephanie Hendrixson describing the cold plate application in the electric vehicle. Image courtesy of Additive Manufacturing Magazine.
The first video shows a design process for a custom cold plate to be created through 3D printing (additive manufacturing) run time is 04:22. The second video shows a practical application of a 3D printed cold plate to cool an inverter in an electric vehicle and runs ~20 min.
An air to water heat exchanger is readily connected to a cold plate by connecting the heat exchanger's outlet port to the cold plate's inlet and the heat exchanger's inlet port to the outlet of the cold plate. The heat exchanger is external to the device(s) being cooled and could be mounted on a cabinet wall. It requires power and a water flow regulator is used to control fluid flow and thereby temperature.
If you're interested in viewing a video on the 3D design of this product, click here.
Sources:
1. https://www.youtube.com/watch?v=qO41S4jG1ew
2. https://www.ntop.com
3. https://www.youtube.com/watch?v=kX-5GIF-97s
4. https://www.additivemanufacturing.media/

When to Use Thermoelectric Coolers
The thermoelectric effect, also called the Peltier effect after its inventor Jean Charles Athanase Peltier, is the direct conversion of temperature differences to electric voltage and vice-versa.
It works by the fact that when two dissimilar conductive or semiconductor materials are fused together to form an electrical junction, and a current is passed through that junction, the material on one side of the junction heats, while the other side cools. This creates heat transfer that can be used for cooling an enclosed space. Since the direction of heating and cooling is determined by the polarity of the applied voltage, thermoelectric devices can also be used as temperature controllers.
Peltier cooling units are mainly used for applications requiring a lesser amount of cooling 100 to 2,750 BTU/hr (~ 30 - 800 W). Unlike conventional cooling units, Peltier devices can be mounted in any position—keeping your condensate management in mind. With a protection rating of IP 66, they can be used both for indoor and outdoor applications.

Cooling Energy Storage Battery Enclosures
A major EV power distribution and charging station manufacturer needed a cooling solution for their energy storage batteries in their power substation supplying power to nearby EV charging stations. They turned to Seifert's Progressive Series using an 8,500 BTU/Hr A/C unit in each enclosure.

Filter Fans
Seifert filter fans feature a robust plastic-molded design with various AC and DC voltage options for power. All filter fan cutout dimensions comply with the market standards. UL listed filter fan packages include IP54 standard version, IP55 and EMC as well as UL type 12 and UL type 3R. Integrated air filters at your system's inlet and outlet ensure that the cabinet remains clear of dust and any other contaminating airborne particles. Mounting our fans into the cutout is a very quick procedure and requires no tools. When necessary, the filters are also easily replaceable.
If you have a question about enclosure cooling for your specific application, Seifert Systems' technical staff would be glad to speak with you. Email us at info.us@seifertsystems.com or call 401-294-6960 .
Please email suggestions for technical subjects you would like to suggest for this newsletter to this link: Newsletter Editor